A 1984 Newspaper Clipping. Oops — What if?
“GM Factory of the Future Will Run with Robots”
New York Times October 20, 1984
Whilst rummaging through my files recently I found an interesting clip about GM and its planned factory of the future program. (We actually cut items from the newspapers in those ancient times.) I recalled my interest about automation in those days because I was in the consulting biz and needed to stay abreast of the latest and greatest manufacturing “stuff.” What could be better than robots at GM?
Quick context
Following WW II, the U.S. was the manufacturing giant. We had tooled-up for the war but did not suffer any severe damage to our facilities. We were, literally, the envy of the world and our three automotive companies, General Motors (GM), Ford, and Chrysler (the “Big Three”), dominated the auto industry.
Japanese cars began to enter the U.S. market during the 1950s and 1960s. The first notable entry was in 1957 when Toyota started selling vehicles in the U.S., followed by other Japanese manufacturers like Honda and Nissan. These early efforts were modest in scale and no real threat to the Big Three.
However, the presence of Japanese cars grew more pronounced in the 1970s, particularly during the oil crisis of 1973. Fuel efficiency and initial quality became more important to consumers than a big car with fins. And once they obtained a foothold they just kept growing in popularity and a real threat to the Big Three.
GM fights back
Since machines were relatively easy to install and the companies and the United Auto Workers were not on the best of terms, it may have seemed to make sense to automate the production of automobiles. The intent was to cut costs and improve quality.
All three played with automation, but only GM went in deep with the Factory of the Future initiative. By “deep” I mean that they spent approximately $90 billion during the 1980s to fully automate some of their factories.
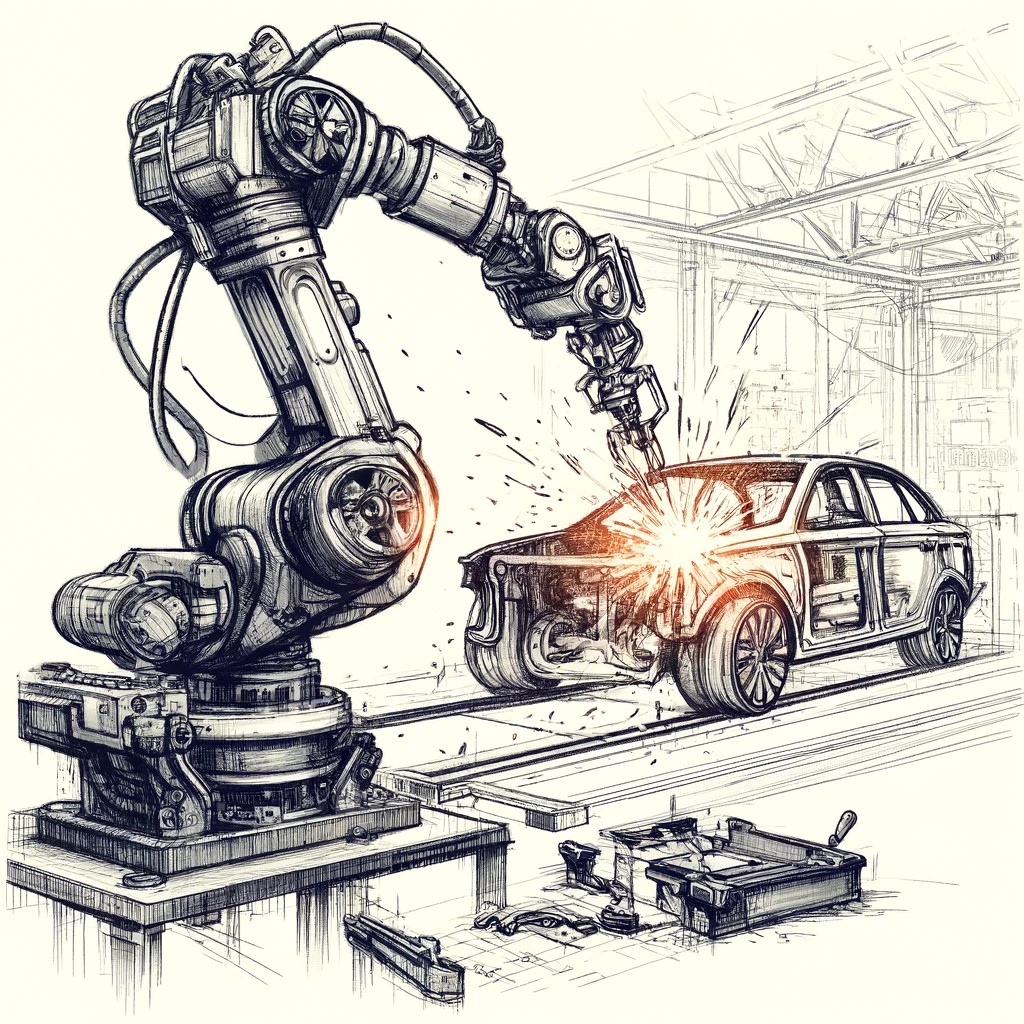
Oops
The initiative had some successes but was not the winning strategy they had hoped for. Toyota, Honda, and Nissan kept growing market share. The factory of the future was widely regarded as an expensive failure.
What went wrong? Here are four things to consider.
1. Overemphasis on automation: GM heavily invested in robotics and other automation technologies but the technology at the time was not as advanced or reliable as needed, leading to frequent breakdowns and disruptions in production. Also, the machines often couldn’t handle the variability in tasks that human workers managed with ease.
2. Neglect of quality and process Improvements: Yes, Japanese competitors were using advanced technology. AND they were also deeply committed to continuous improvement processes like Kaizen and the Just-In-Time (JIT) inventory system. GM, in focusing primarily on automation, initially overlooked the importance of these process improvements.
3. Cultural and Workforce Challenges: The implementation of new technologies required significant changes in work practices and roles, which met with resistance from GM’s workforce. Japanese firms, in contrast, typically had more flexible work practices and a stronger culture of adaptation and continuous improvement.
4. Insufficient Training and Integration: The integration of advanced robotics into GM’s existing factories often lacked sufficient planning and training. Workers and managers needed more skills to effectively operate and maintain the new automated systems.
What if?
By now you know that I’m looking into the combination of five thinking disciplines to develop a “prepared mind.” Here are some thoughts about GM’s initiative forty years ago.
1. Systems Thinking: This approach would have encouraged GM leaders to examine the manufacturing process as a complex system comprising various interrelated components—technology, people, processes, and culture. This might have led to a more integrated and holistic planning process.
2. Strategic Thinking: GM’s leadership might have recognized that the real competitive edge of Japanese automakers wasn’t just automation but their entire production philosophy, including workforce involvement, quality management, and lean manufacturing.
3. Skepticism: A skeptical approach would have been invaluable in challenging assumptions about the benefits of heavy automation and could have promoted more rigorous testing and gradual implementation of new systems.
4. Design Thinking: If GM had employed design thinking, they might have more closely considered the needs and capabilities of their workforce when designing the new automated systems. This could have led to technology adoption that was more user-friendly and better supported by the workers.
5. Foresight: Foresight might have highlighted the importance of flexibility in manufacturing processes to adapt quickly to future challenges and opportunities.
It’s always easy and fun to criticize the past. What about your future? Want to expand your thinking beyond your current functional discipline? You need a Prepared Mind and maybe we can help.
Cheers,
Bill